When should I use Ductile Iron Piles?
- Tight access, limited laydown area or variable grades.
- Vibration-sensitivity.
- Low overhead clearance restrictions (18 feet and above).
- Building additions.
- Deep bearing layers that result in pile splicing or slow pile installation.
If you are considering these techniques for your project:
- Micropiles.
- Helical Piles.
- Short piles where installation vibrations, speed or project site constraints or size makes a good fit.
- Long piles where elimination of splicing or working with small sections maximizes the benefit.
- Poor soil conditions – deep soft soils, fills and/or organics
- Vibration sensitivity
- Adjacent structures
- Difficult access and constrained sites
- Low overhead
- Variable grades
Benefits of Ductile Iron Piles
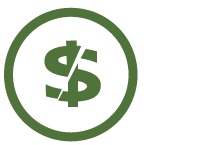
Cost-Effective
Often provide 15-25% cost savings over drilled micropiles and other deep foundation systems.
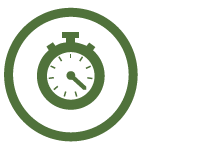
Rapid Installation
Daily production rates range from 600 to 1,400 feet per crew.
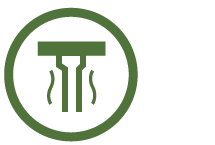
Low Vibration
High-frequency, low amplitude driving energy results in low vibrations allowing installation to occur within and adjacent to existing structures.

High Load-Carrying Capacity
Working capacities range from 25 to more than 100 tons in compression, and often 20 to 50 tons in tension.
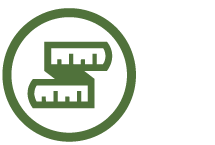
Depth Flexibility
The Plug & Drive System allows for easy length adjustments in the field when faced with fluctuating bearing layer depths. The system can easily be installed to 20 feet or more than 100 feet by simply adding additional DIP sections with the Plug & Drive moment-resisting, drive-on connection.
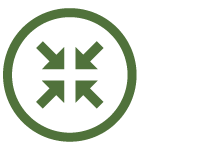
Easy Access
Mobile track-mounted equipment and modular pile sections allow for rapid work in constrained areas, sloping ground and limited lay-down areas.
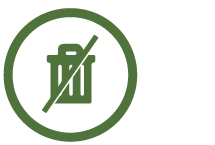
Minimal Waste
The system generates virtually no waste since the cut-off section of pile is used as the starter pile for the next location. This is a significant advantage over traditional steel piles (pipe or H-piles) on sites with varying rock elevations that would result in wasted cut-off material or having to add in costly field splicing. Ductile Iron Piles eliminate these concerns completely.
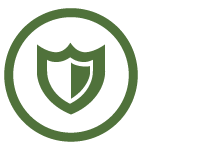
Quality Installation
Load-bearing capacity and pile length are determined on-site through load testing and monitoring of penetration resistance and driving.
Typical Applications
Ductile Iron Piles provide reliable support for commercial, industrial, residential and infrastructure projects including new construction, additions to existing facilities and interior retrofit applications. Ductile Iron Piles provide cost-effective deep foundation solutions for foundation and floor slab support to resist compression, tension and lateral loads. The system offers high value solutions for the following challenges:
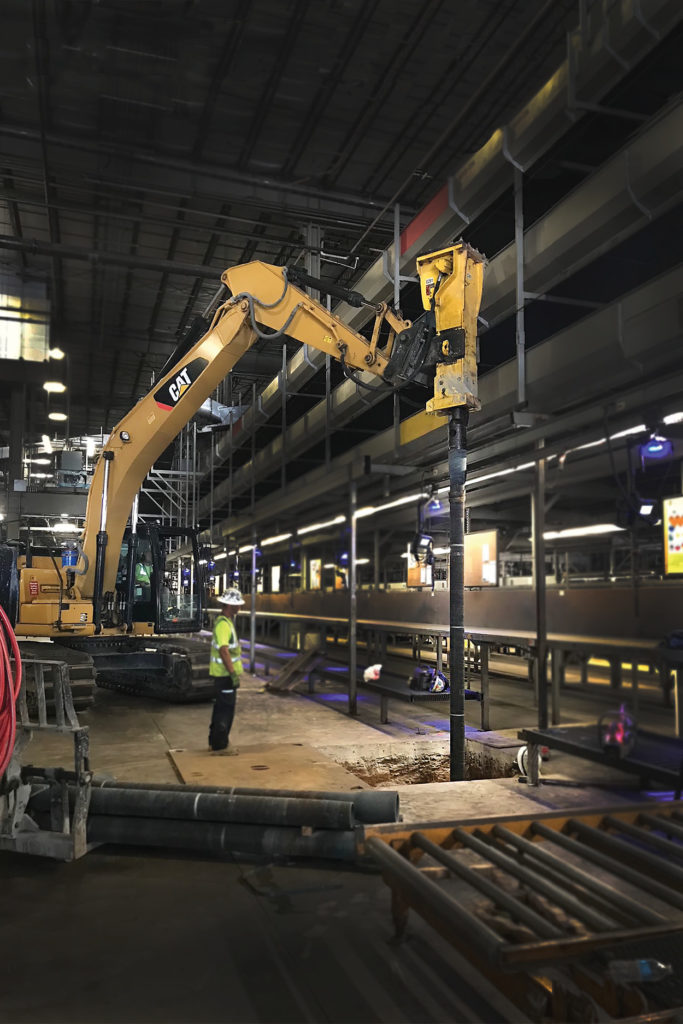
Low Overhead
Deep foundation options for interior applications are often limited due to access and overhead obstructions. Ductile Iron Piles are uniquely positioned to provide a rapid, cost-effective solution for interior work in commercial, industrial, warehousing and other applications. Ductile Iron Piles are a modular system with pile sections that are typically between 16 and 18 feet (5.0 to 5.5 meters) in length. The innovative plug and drive (bell – spigot) joint allows rapid connection of piles to achieve sizable depths even with limited overhead clearance. Further, pile sections can be cut in half or thirds and connected with drive-on couplers to allow work in limited overhead conditions. Installers of the Ductile Iron Pile system routinely work within overhead clearances of 18 feet or above. By providing higher capacities than light-duty helical piles and less cost and faster installations than large diameter helical piles and micropiles, Ductile Iron Piles offer a high value deep foundation option when working in low-overhead conditions.
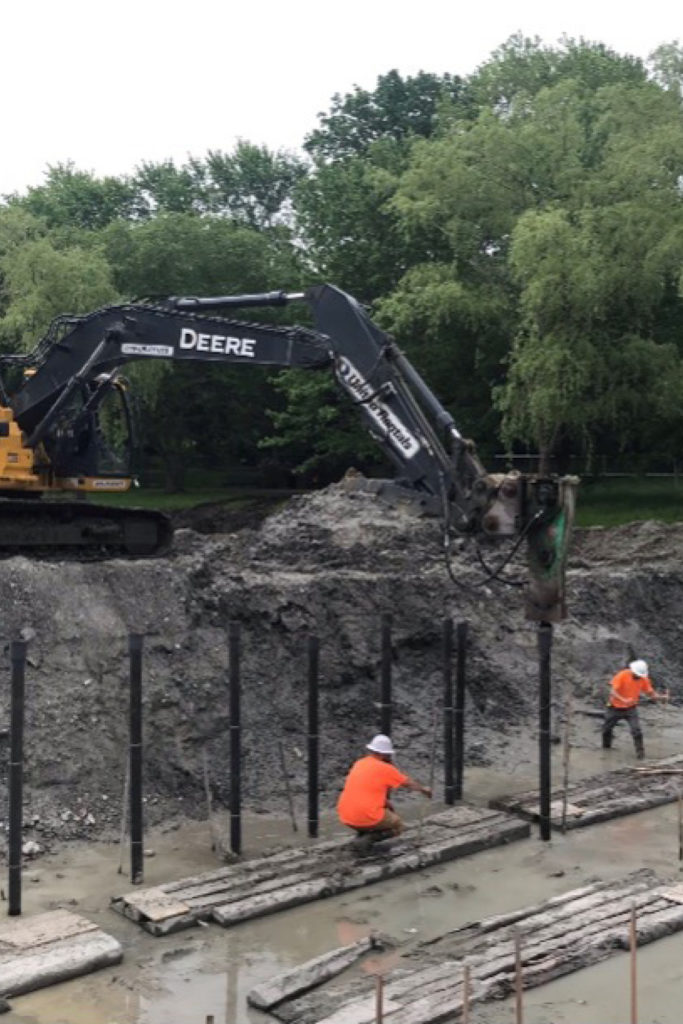
Soft Soils
Deep foundations have long been used to penetrate and bypass soft soils to prevent unacceptable settlement or even bearing capacity failure of supported structures. Ductile Iron Piles are driven rapidly through soft soils to transfer structural loads to underlying stronger soils and, in some cases, can be advanced (pushed) using only the weight and crowd force of the excavator and percussion hammer. Ductile Iron Piles are specifically designed to resist buckling of the pile surrounded by soft layers at design loads typically ranging from 25 to 100 tons. The QC observation during installation allows for the detection of the soft zone to verify the piles develop capacity in competent ground conditions below soft zones of soil. With the modular nature of Ductile Iron Piles, added pile lengths to penetrate deeper-than-anticipated soft zones is easily achieved by adding pile sections using the rapid, moment-resisting Plug and Drive connection. This eliminates the need for splicing or welding additional pile sections that would be required with traditional driven pile methods.
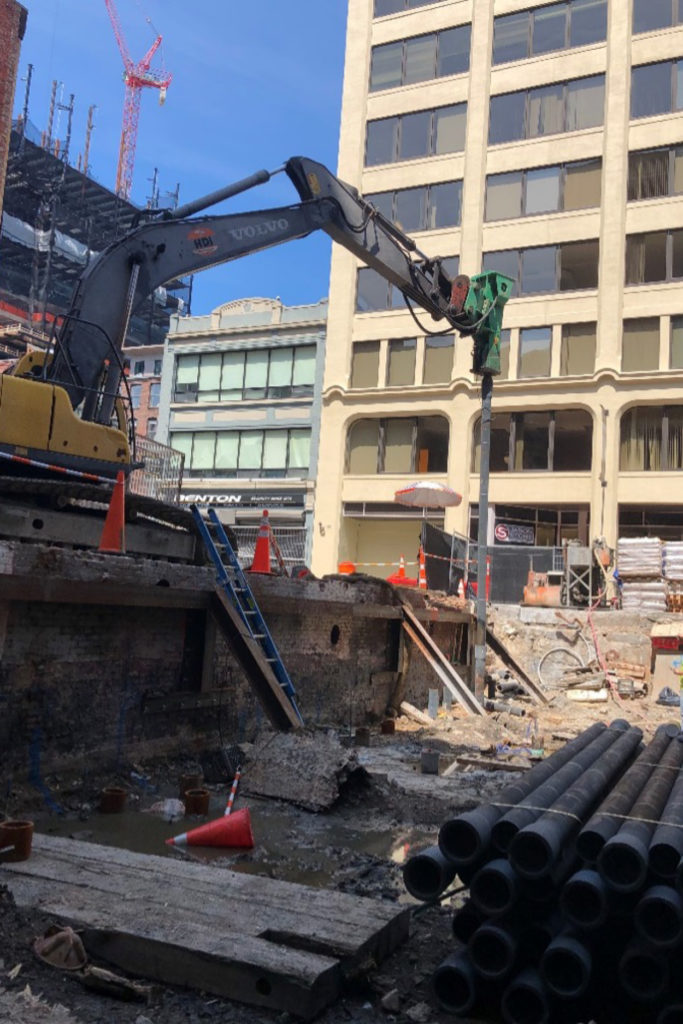
Urban Fill
Development of urban properties is often complicated by the presence of urban fill below grade. Remnants of past structures on the site often result in obstructions buried within the fill, like pieces of concrete, brick, wood, and various other items. Common remedies include removal and replacement of the unsuitable soils, ground improvement, or deep foundations. Removal and replacement often requires extensive support-of-excavation to avoid impacts to adjacent structures and may require expensive handling of contaminated soils. Traditional deep foundations or ground improvement must penetrate the urban fill and may require expensive drilling equipment capable of delivery high-torque drilling for larger diameter elements. In many cases, the cost for pre-drilling to penetrate and create a clear path for foundation elements drives foundation costs to extreme levels. Small diameter Ductile Iron Piles driven with high frequency, percussion energy have a track record for successful installations on fill sites where the piles effectively displace small obstructions and penetrate the urban fill. When pre-drilling is required, pilot hole diameters for Ductile Iron Piles are much smaller than pre-drill diameters required for other foundation elements, resulting in smaller equipment needs, less effort, and less cost. Additionally, when unexpected obstructions are encountered at sites that result in shallow pile refusal, the modular Ductile Iron Pile system results in less waste when the refused pile must be abandoned. New offset pile locations can easily be started with the remaining, above-grade portion of any abandoned Ductile Iron Pile.

Variable Bedrock
In many geologies, the strength and elevation of competent bedrock makes for great uncertainty in the predicted lengths of deep foundation systems. This is particularly challenging for driven pile systems, which are commonly ordered and delivered in pre-determined lengths. Changes in the bedrock elevation can often result in the need for waiting for additional material combined with slow and costly field splicing when rock is deep. Alternatively, significant wasted pile material can result when shallow rock is encountered, and excessive pile lengths are cut-off. These risks are substantially reduced with Ductile Iron Piles – a modular system with pile sections that are typically between 16 and 18 feet (5.0 to 5.5 meters) in length. The innovative plug and drive (bell – spigot) joint allows easy and rapid connection of pile sections to achieve virtually any length and eliminates field splicing to easily solve the issue of longer piles. Further, the modular nature of Ductile Iron Piles significantly reduces risks associated with large amounts of pile waste. When piles reach early refusal or “set,” the remaining section of pile is cut off and used as a starter pile section on the next pile, thereby eliminating the material waste. Unused pile sections can also be easily re-used on future jobs to allow specialty contractors to have confidence in ordering materials. For sites with variable bedrock, Ductile Iron Piles greatly reduce material waste and lead to the efficient use of pile materials.
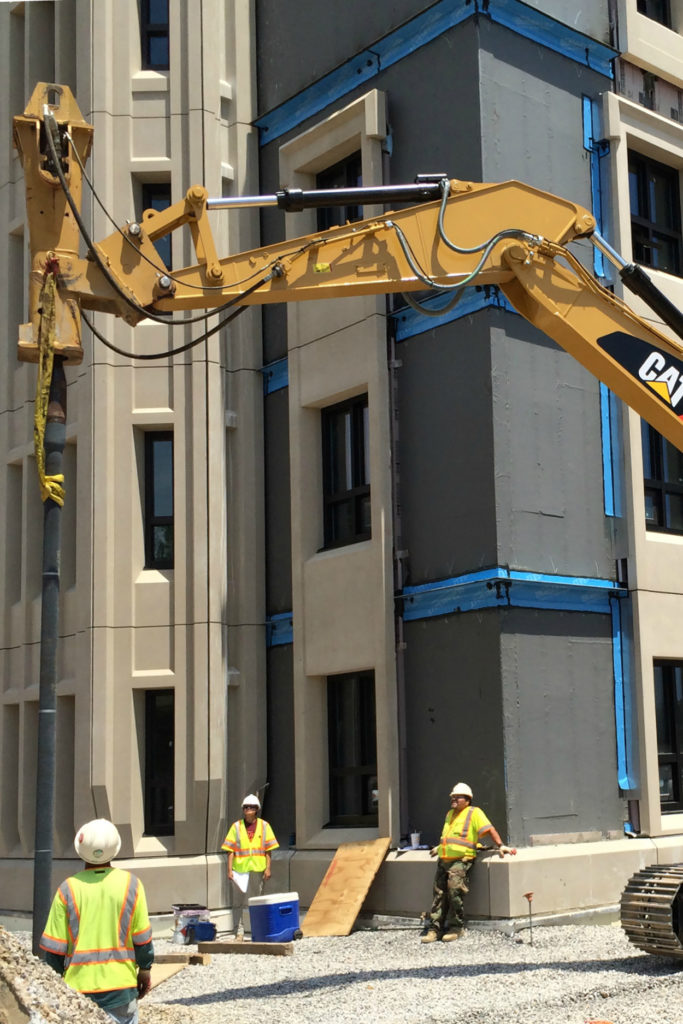
Low Vibrations
Ductile Iron Piles are ideally suited for urban conditions or interior construction where vibration levels are a concern. Traditional driven piles use large hammers that generate high amplitude and low frequency vibrations that travel long distances, often exceed vibration thresholds and can cause vibration-related damage to nearby structures. Unlike traditional driven pile installation, Ductile Iron Piles are installed with a standard breaker (percussion) hammer. The percussion hammer delivers high frequency, low amplitude vibration levels. The hammer energy levels are considerably less than a traditional driven pile. Typical peak particle velocities often range from only 0.5 to 1.5 inches/second within a few feet of installation and dissipate rapidly at distances of only 10 or 20 feet away from the installation. With these low vibration levels, Ductile Iron Piles are often a preferred approach for projects featuring building additions, urban construction and interior, low-overhead projects.
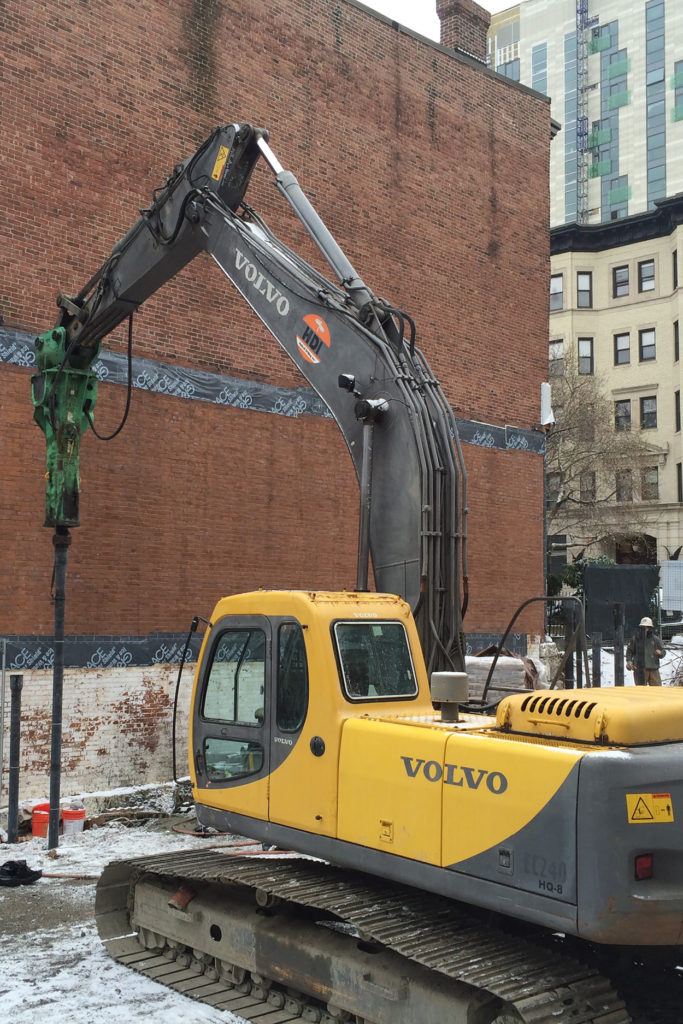
Adjacent Structures
Construction of building additions often requires foundation systems capable of generating low vibrations during installation and working in close proximity to existing buildings for new foundation work. Ductile Iron Piles are installed using medium-sized excavators (i.e. 20 to 30 tons) that are able to maneuver close to existing buildings on sites with tight access. Driving is performed using a standard breaker (percussion) hammer that generates high frequency, low amplitude energy. The high frequency energy results in limited vibrations to facilitate pile installation adjacent to existing buildings. The combination of the ease of access and low vibrations make Ductile Iron Piles a good solution for new projects adjacent to existing structures.
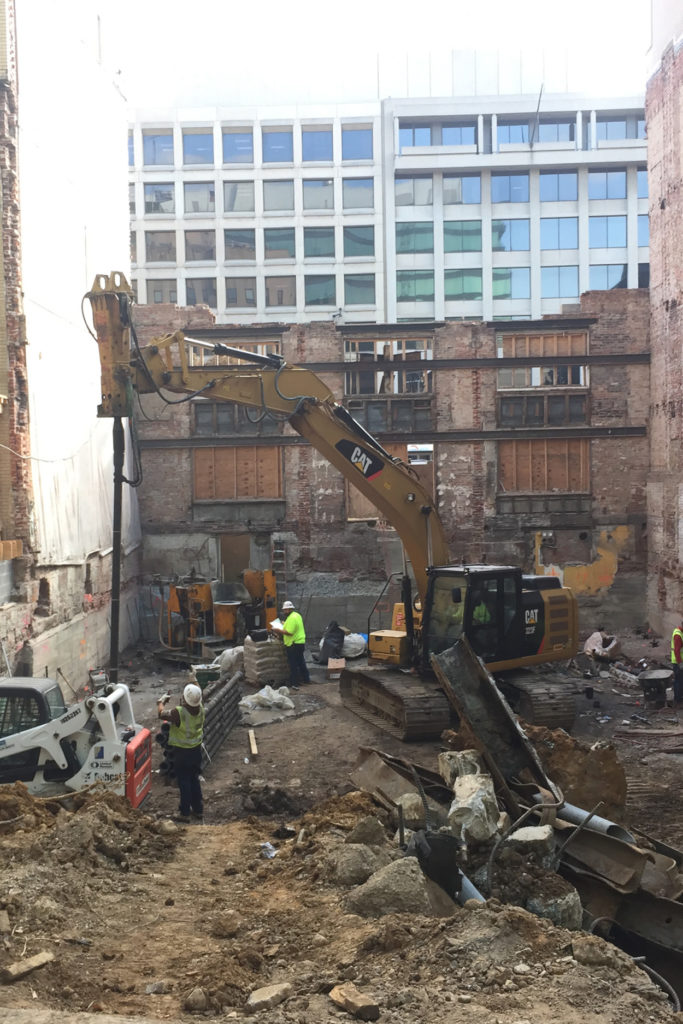
Constrained Sites
Projects routinely require work on constrained sites including small site footprints in urban settings, at industrial or commercial facilities with obstructed access or sites requiring work at various grades. Ductile Iron Piles are a preferred solution to easily accommodate the various site constraint challenges. With the modular pile sections, transportation in small bundles makes for ease of delivery and stacking on tight sites to limit staging area needs. The modular pile sections incorporate the Plug and Drive connection to install piles to virtually any practical length while only managing sections of less than 20 ft in length, significantly reducing laydown requirements compared with traditional driven piles, drilled shafts or augercast piles. The excavator-percussion hammer combination limits the amount of space for equipment compared with other larger vertical mast rigs and allows easy maneuverability and the ability to install piles from various grades across the site. The low vibration levels during installation reduce the potential for damage during installation. For many reasons, Ductile Iron Piles offer significant benefits on challenging sites.
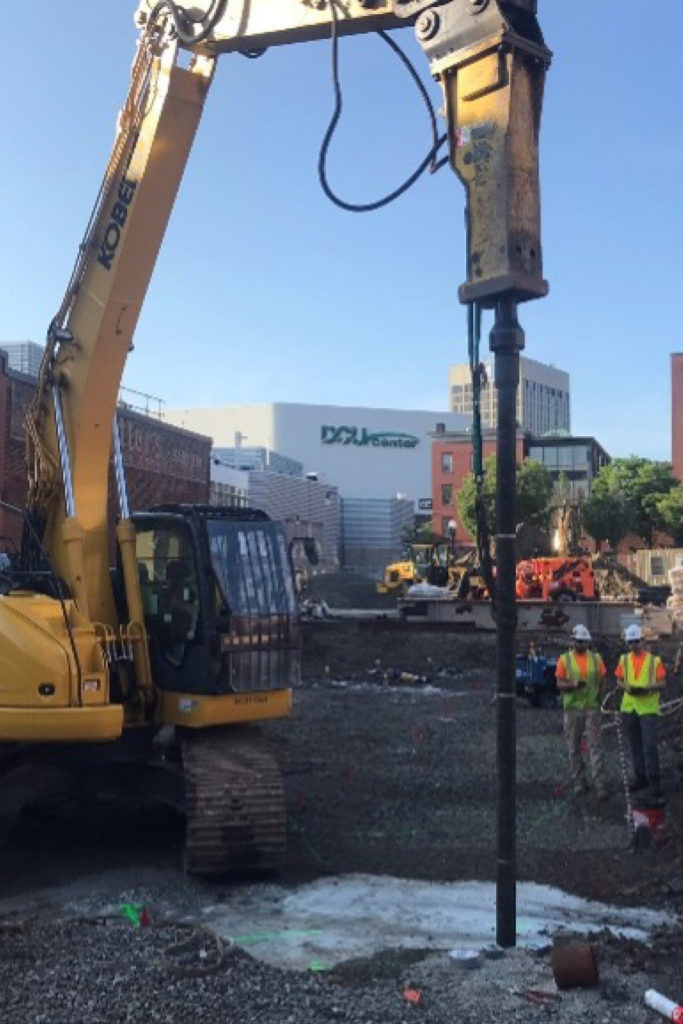
Organics
Organic soils (peat, organic silt/clay) are often soft and highly compressible and are subject to long-term secondary compression (creep) and material degradation. Depths of organic deposits can be highly variable across a site and are not often discovered until foundation installation. Building sites with organic soils typically require deep foundations to transfer foundation and slab loads below the organic zones. Ductile Iron Piles have been used extensively on sites with organic soils. The Ductile Iron Piles are designed to resist buckling of the pile in the soft layer. The QC observation during installation allows for the detection of the organic zone extent to verify the piles develop capacity in competent ground conditions below the organics. With the modular nature of the piles, added pile length to penetrate deeper-than-anticipated organic zones is easily achieved by adding pile sections using the rapid, moment-resisting Plug and Drive connection.
Frequently Asked Questions
What are Ductile Iron Piles (DIPs)?
Ductile Iron Piles (DIPs) are modular, low vibration driven piles manufactured from ductile iron via a centrifugal-casting process. With standard DIP lengths of 16.4 feet (5 m), the piles employ a unique Plug & Drive connection system enabling additional pile lengths to be quickly added without added mechanical connections or field splicing. Piles of varying lengths can be driven to depth and the cut-off section is used as the lead section for the next pile, resulting in minimal or no waste.
Where have DIPs been installed?
Tens of millions of feet of DIPs have been installed throughout the world over the past three decades. DuroTerra specializes in Ductile Iron Pile projects primarily in the U.S., Canada and Latin America.
When should you consider using Ductile Iron Piles?
If your project has:
- Tight access, limited laydown area or variable grades
- Vibration-sensitivity
- Low overhead clearance restrictions (18 feet and above)
- Building additions
- Deep bearing layers that result in pile splicing or slow pile installation
You are considering the following techniques:
- Micropiles
- Helical piles
- Short piles where installation vibrations, speed or project site constraints or size makes DIPs a good fit
- Long piles where elimination of splicing or working with small pile sections maximizes the benefit
You encounter one or more of the following challenges:
- Poor soil conditions – deep soft soils, fills and/or organics
- Vibration sensitivity
- Adjacent structures
- Difficult access and constrained sites
- Low overhead
- Variable grades
What are the primary advantages of using Ductile Iron Piles?
- Cost-Effective: Often provide a 15-25% cost savings over drilled micropiles and often other traditional deep foundations
- Rapid Installation: Daily production rates typically range from 600 to more than 1,400 feet per crew
- Low Vibration: High-frequency driving process results in low vibrations allowing installation to occur within or adjacent to existing structures
- High Load-Carrying Capacity: Working capacities range from 25 to more than 100 tons in compression, and often 20 to 50 tons in tension
- Flexibility: The Plug & Drive connection system allows for easy length adjustments in the field when faced with fluctuating bearing layer depths
- Easy Access: Mobile equipment and short pile sections allow for rapid work on constrained sites, variable working grades and limited lay-down areas
- Minimal Waste: Once completed, the pile is cut-off and the cut-off section including the bell is used as the starter pile for the next location, yielding virtually no waste
- Quality Installation: Pile capacity and length are determined on-site through load testing and monitoring of penetration resistance and driving
What are typical applications for Ductile Iron Piles?
Most common applications include:
- Building Foundations
- Floor slabs
- Tension
- Infrastructure Foundations
- Tanks
- Solar
- Wind
- Underpinning
Can Ductile Iron Pile systems resist both compression and tension loads?
Ductile Iron Piles are used to resist both compression and tension loads. Compression loads are resisted through either end-bearing on dense/hard soil or rock or through frictional resistance developed with a grout-to-ground bond zone within competent soil. The bond zone is created when the Ductile Iron Pile is driven with a patented oversized grout cap and grout is simultaneously pumped to fill the annular space. Tension loads are resisted using the same grout-to-ground frictional mechanism engaged in tension by using a high-strength threaded reinforcing bar centralized in the pile as a reaction to resist uplift loads.
What types of soils can Ductile Iron Piles be used in?
Ductile Iron Piles are well-suited for supporting loads in a variety of problematic soil conditions including both cohesive and non-cohesive soils. Typical geotechnical conditions requiring the use of Ductile Iron Piles consist of:
- loose or soft undocumented fill
- loose sand to medium dense sand
- soft and compressible clay and silt
- peat and organics
The DIPs are designed and installed to penetrate these problematic soil conditions and develop resistance through either end-bearing on competent soil or rock or through frictional resistance afforded by a grouted bond-zone formed along the portion of the pile installed in the competent soils. Ductile Iron Piles developing capacity in end-bearing are installed to achieve a particular “set” criteria while penetrating into a dense layer (i.e. very dense sand, glacial till, hard clay, etc) or refusal on rock. Friction DIPs require the presence of a loose to very dense granular soil or firm to hard cohesive soil to develop a grouted bond zone capable of providing sufficient frictional resistance with the soil to achieve the design capacity.
What are the skin friction values for cohesive and non-cohesive soils?
Allowable skin friction values for the grout-to-ground interface depend on the specific soil condition in which the bond is being developed as well as the consistency or density of the layer. The following figures developed by the pile manufacturer from decades of load test experience provide approximate ranges of skin friction values for cohesive and non-cohesive soil layers.
Do Ductile Iron Piles offer higher corrosion resistance to conventional micropiles or steel piles?
Yes, DIPs do offer superior corrosion resistance. The materials used to manufacture the pile contain higher silicon and carbon contents when compared to traditional steel products, resulting in greater corrosion resistance. The excess carbon acts as a filtering mesh preventing corrosion penetration, while the silicon causes the formation of a durable protective iron silicate outer layer. Sacrificial corrosion rates are well established in the Austrian standard ONR 22567 (as determined by MA39, i.e. Material Testing Authorities, Vienna). Ductile Iron Pile designs must consider the corrosion susceptibility of a site and either reduce the allowable design values based on a reduced pile sectional area (i.e. sacrificial layer) or incorporate exterior grout to reduce corrosion concerns.
How much vibration and sound does the installation of Ductile Iron Piles generate?
DIPs are installed using a hydraulic hammer that delivers high-frequency, low-amplitude impact ramming energy during the driving process. The high frequency energy combined with the penetration of relatively small diameter DIPs result in low vibrations that dissipate rapidly during driving. Vibration monitoring on typical sites show peak particle velocities on the order of 0.25 to 1.0 inches/second within a few feet of the pile installation. These vibration levels dissipate rapidly with distance and are often not perceptible at only short distances away from the installation. Many DIP projects have been successfully completed with installation occurring within existing (and active) facilities and within 18 inches of existing buildings. The limitation is often more related to equipment access than vibrations during installation. Sound levels are comparable with other earthwork equipment operations.
Can DIPs be installed on a constrained site or site with low overhead conditions?
Ductile Iron Piles are often a preferred solution on constrained sites for multiple reasons. Transportation and staging of the piles are easily managed because of the 5m (16.4 ft) standard lengths which allows for easy delivery access in urban environments and limited laydown requirements. The single piece of tracked equipment can operate within limited access areas, excavations or within areas with varying grades. As a result, DIPs are an ideal solution for constrained sites or those challenged with access issues. Further, the system is often installed in areas with low overhead conditions. The pile sections can be cut in half or thirds and a drive-on coupler is used to create a moment resisting connection, allowing the piles to be installed in 18 feet or greater overhead clearance. The system is often a preferred approach in low overhead conditions like warehouses, industrial facilities and commercial buildings because of the speed of installation and high capacities combined with the clean installation process and low vibrations.
How can I determine whether Ductile Iron Piles are a viable solution for my project?
DuroTerra representatives are pleased to provide technical feasibility and constructability assessments to evaluate whether Ductile Iron Piles are a good match for your project. Our engineers can assist you with preliminary feasibility designs based on geotechnical information and structural plans. You can complete the project feasibility assessment link on the website, drop us an email at
or call us directly at 781.817.6053.
How can I use Ductile Iron Piles for my project?
Ductile Iron Pile project design and installation is handled through DuroTerra’s network of regional designers and installers. If you are interested in evaluating Ductile Iron Piles for your project, receiving a proposal for installation or interested in learning more about designing or installing the system, please complete the project feasibility assessment link on the website, drop us an email at
or call us directly at 781.817.6053.
What is DuroTerra’s role?
DuroTerra is the distributor of TRM’s Ductile Iron Piles in North America. We continue to partner with leading engineers and specialty contractors throughout North America who specialize in DIP design and installation, providing customers with a more efficient, cost-effective deep foundation alternative for your projects. DuroTerra works closely with all of our customers including geotechnical engineers, structural engineers, owners, general contractors and architects to evaluate feasibility of the system. As projects evolve, we work closely with our DIP designers and installers to provide technical and construction support to ensure that proper design and installation methods are executed.