Ductile Iron Pile Products
Ductile Iron Piles (DIPs) are a simple, fast and highly effective modular, low-vibration driven pile system comprised of high-strength ductile cast iron. Pile sections are connected by a proprietary Plug & Drive joint system, eliminating the need for field welding and splicing while providing a high degree of stiffness and full moment capacity. With the use of an excavator fitted with a hydraulic hammer, piles are installed in quick succession leading to fast and easy installation.
Ductile Iron Piles are manufactured by Tiroler Rohre, GmbH of Austria from ductile cast iron, which provides high-impact resistance to the low amplitude, high frequency installation energy. The material also exhibits high ultimate strength, elastic limit and ductility as well as superior corrosion resistance when compared with traditional steel piles.
Ductile Iron Piles are well-suited for supporting loads in a variety of problematic soil conditions including both cohesive and non-cohesive soils and can also resist compression and tension loads.
VIEW THE DUCTILE IRON PILE BROCHURE
Piles & Accessories
End-bearing & Friction Piles
Ductile Iron Piles have been manufactured by Tiroler Rohre GmbH (TRM) in Austria for over 35 years. Each modular pile section features a Plug & Drive connection consisting of a tapered socket with an internal shoulder for full engagement at one end and a tapered spigot at the other end. This allows the individual pile sections to be connected together to form a pile shaft of virtually any length without the use of special tools. The connection is formed by elastic deformation of the ductile iron and by cold welding of the friction surfaces. This joint exhibits high-compressive strength and superior resistance to bending, such that the rotational stiffness of the joint is greater than the main pile shaft. This connection method eliminates the need for threads, couplers, pins and keys and field welding/splicing on the job site.
Ductile Iron Pile installation methods consist of either dry (no exterior grout) or wet (continuous grouting operation during installation) installations. Additionally, both options can develop load-carrying capacity in either friction in competent soils, end-bearing on very hard ground/rock or a combination of both. The specific pile materials and accessories depend on the type of installation and mechanism for load resistance. Both methods utilize a unique combination of installation speed and high capacity that results in a highly cost-effective deep foundation system.
End-Bearing Piles
Ductile Iron Piles installed for end-bearing are driven through compressible and unsuitable soils to transfer their load to a hard stratum below. They derive most of their load-carrying capacity thru resistance along the portion of the shaft in competent soil and at the toe of the pile. End-bearing piles may be installed using a dry installation method without continuous grouting during installation (as pictured) or as the wet installation method with oversized pile shoes and continuous pumping of exterior grout.
Friction Piles
Ductile Iron Piles installed as friction piles penetrate poor soil conditions and develop the majority of the load-carrying capacity in frictional resistance along the perimeter of the pile shaft in the competent strata. While some friction piles use a dry installation method (without continuous grouting) and develop strength through the interface between the soil and the roughened exterior of the ductile iron pile shaft, the majority of friction piles utilize oversized conical drive shoes and exterior grout to encapsulate the pile during driving for very effective grout to ground bonding. The oversized cap results in significant expansion (and densification) of the competent soil while the grout-to-ground bonding provides a highly efficient mechanism for load transfer.
Ductile Iron Piles Material Specifications
Ductile Iron piles are typically manufactured in standard (usable) lengths of 5 meters (16.4 feet). Overall pile lengths including the bell (socket) are slightly longer and range from 16.9 ft (5.15 meters) to 17.2 ft (5.25 meters). Piles are available in multiple diameters and wall thicknesses to suit project needs. Details of the dimensional characteristics are provided below:

All Ductile Iron Piles are manufactured in 5 m (16.4 ft) lengths.
Product Accessories
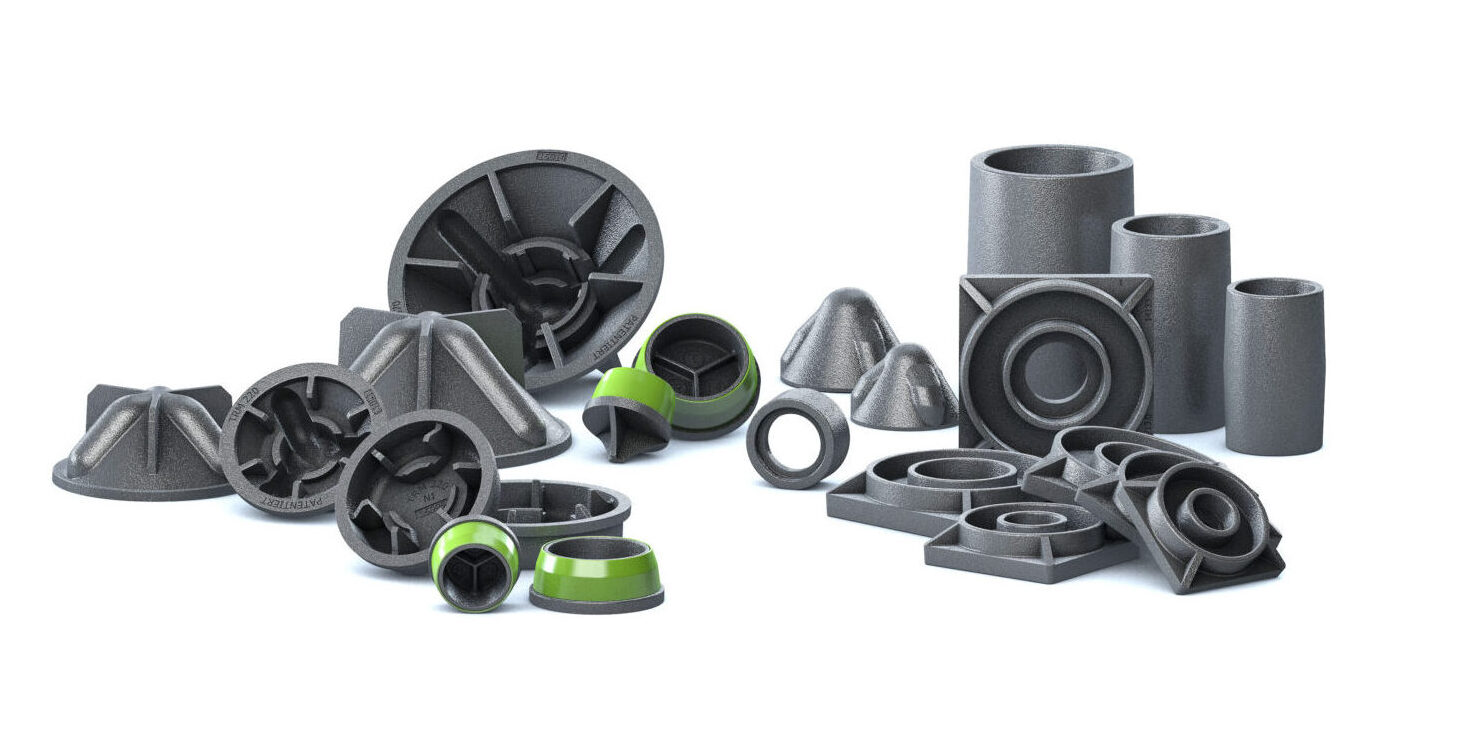
The same pile sections are used for both end-bearing and friction applications. However, the various accessories are specific to the type of application and method for loading resistance:
Flat End Drive Shoe
Standard drive shoes for piles installed using the dry installation method.
Rock Point
Alternative drive shoes for dry installation methods, typically for end-bearing (non-friction) piles, used when driving through harder material such as partially weathered rock or glacial till.
Heavy-Duty (HD) Flat Drive Shoe
Heavy-duty (HD) flat drive shoes for dry piles are used when driving through hard conditions such debris fill, partially-weathered rock or glacial till for greater durability during driving. HD caps are also used in very soft soils to reduce the potential for dislodging of the drive shoe during driving.
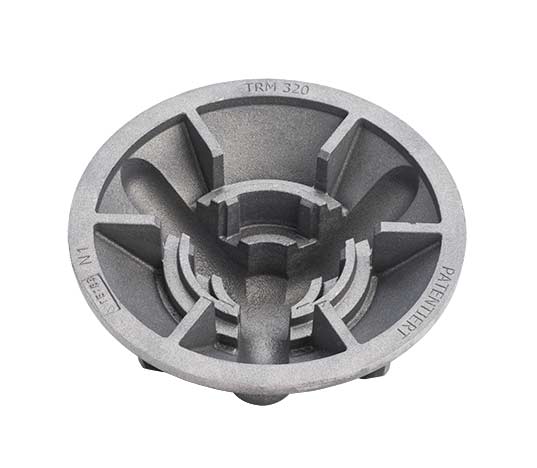
Conical Grout Shoe
Conical grout shoes are used for installation of exterior grouted (wet installation) piles. Grout shoes have a larger diameter than the pile, creating an annulus around the pile which enables the placement of fine-aggregate concrete (grout) to encapsulate the full length of the pile shaft. Grout shoe diameters range from 150 mm (5.9 in) to 370 mm (14.6 in). Appropriate shoe sizes depends on the pile size, soil conditions, hammer size and desired design capacity.

Coupler
A coupler is used to connect two partial pile sections in place of the standard spigot and socket connection. Couplers are most often used when piles are driven in low headroom environments where pile sections must be cut for overhead access. Couplers are not required for standard applications with full-length pile sections utilizing the Plug and Drive connections.
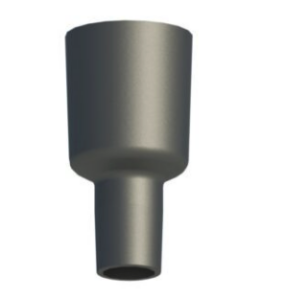
Converter
A Converter is used to switch from a Series 118 pile to a larger Series 170 pile. The Plug and Drive converter is installed into the bell of a Series 118 pile and a new Series 170 pile is then inserted and driven. The converter is often used for situations where a larger pile size is required at shallow depths to resist lateral loads, but the axial capacity does not require the larger pile for the full length.

Drive Shanks and Grout Box
A drive shank is a specialized attachment that facilitates the driving of the piles using conventional hydraulic percussion (breaker) hammers. Drive shanks are specially fabricated and hardened to withstand the high driving stresses during installation. Drive shanks are available as 1) solid or dry shanks for installation of dry piles (ungrouted during driving) and 2) wet or grouting shanks to facilitate grout injection into the pile interior during installation of grouted piles. The grout box is designed to surround the wet shank and provide a grout reservoir during grouted pile installation. A wet shank and grout box are used in concert.
Manufacturing Process
Advanced Techniques
Ductile Iron Piles are comprised of grey cast iron, which has been used for commercial pipeline construction since the early 1800s.
Historically, cast iron or grey cast iron was produced in a lamellar form. The material was often brittle and exhibited low strength and impact resistance. Advancements over a half-century ago led to the development of spheroidal or ductile cast iron by adding magnesium to the cast iron before pouring to produce crystallization of graphite in spheroidal form (Figure 2). The development of spheroidal graphite cast iron led to more desirable material properties including improvements in the ultimate and yield strength, tensile and flexural strength, improved impact resistance for drivability and toughness, while maintaining cast iron qualities including machinability and cast-ability.
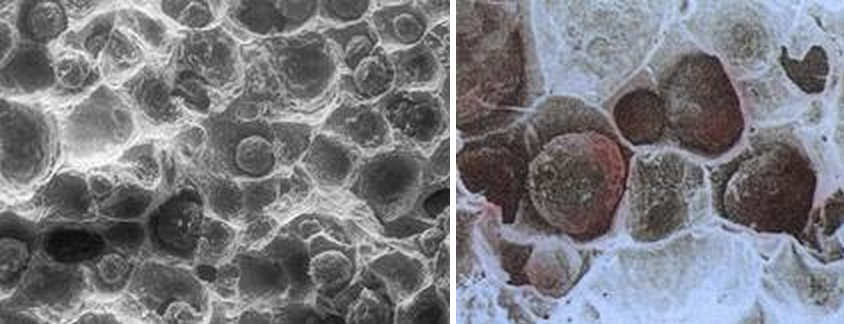
Spheroidal Graphite (Ductile Iron) Detail
During manufacturing of the Ductile Iron Piles, the ordinary grey or lamellar graphite undergoes a sophisticated manufacturing process that transforms it into spheroidal graphite or ductile cast iron. This process drastically improves the cast iron’s impact resistance, ductility, tensile strength and flexural stiffness.
The ductile cast iron material used in the piles contains a high recycled content and is comprised of: 90-95% scrap metal iron, approximately 3.7% carbon, and approximately 2.7% silicon.
Ductile Iron Piles are manufactured by Tiroler Rohre GmbH (TRM) in Austria. Ductile cast iron used in the fabrication of the piles undergoes a sophisticated centrifugal- or spun-casting manufacturing process to transform the raw recycled material into the finished product. The ductile iron piles are factory prefabricated to precise tolerances. Standardization results in the materials being subject to strict control of its chemical composition and its mechanical properties throughout the fabrication process.
Download the Manufacturer Brochure
The manufacturing process employs a quality assurance system that is certified in compliance with ISO 9001:2000 “Quality Management Systems”. Further, a variety of other European inspections and certifications are deployed at key stages throughout the manufacturing process to provide regular control of the product and prefabrication process:
- Standard BS EN 10204 inspection process
- ONCERT certification (ONR 22567 regulation)
- European Technical Approval (ETA-07/0169)
Installation & Equipment
How DIPs Are Implemented
Ductile Iron Piles are installed using an excavator-mounted hydraulic hammer fitted with a special drive adapter that drives the pile into the ground using a combination of the percussive energy from the hammer and the excavator crowd force. Two main types of installation methods exist for the Ductile Iron Piles: Non-grouted (dry) DIPs and exterior grouted DIPs. While the same Ductile Iron Piles are used in each system, the installation process and accessories do vary depending on the method selected for installation.
Non-Grouted Piles
1) Ductile Iron Piles installed using a non-grouted or dry approach begin by first cutting the taper off the first pile section and inserting a flat or pointed driving shoe over the end of the hollow pile.
2) The 5 meter pile section is then positioned vertically (or at the appropriate batter angle if applicable) and driven into the ground using high-frequency impact energy delivered from a hydraulic hammer. The pile is driven until the belled Plug & Drive socket end is nearly at the working grade. The driving resistance (time required to drive each meter increment) is measured during driving.
3) A second DIP section is then lifted into place so that the tapered or spigot end of the second DIP section is inserted into the socket end of the existing pile.
4) The driving process is repeated.
5) This process continues until the pile terminates on refusal or achieves the required driving criteria (typically 1 inch in 50 seconds) or develops sufficient length to achieve the frictional capacity along the roughened Ductile Iron Pile surface.
6) When interior grout is being used, the grout is placed either after the pile achieves the required set or later in the process after multiple piles have been installed. Note that the reference to non-grouted pile refers to the use of the grout during the driving to fill the exterior annular space. It is almost always the case that non-grouted piles are grouted on the interior for added strength and corrosion resistance.
Exterior Grouted Ductile Iron Piles
1) Ductile Iron Piles installed using an exterior grouted approach begin by first cutting the taper off the first pile section and then inserting a specially-designed patented conical grouting shoe over the end of the pile. The conical -grouting shoe is designed specifically for grouting applications and is larger in diameter than the outside pile diameter to create an oversized annular space around the pile that facilitates grout encapsulation around the exterior of the pile. The unique grouting method allows grout to be pumped directly to the base of the pile to ensure grout volume at the critical locations in the pile (compared with gravity fed pile systems that “pull-down” the grout in the pile with no way to verify the continuity of grout to the bond zone.
2) The pile is then driven into the ground using high-frequency impact energy delivered from the hydraulic hammer using a specially-designed grout driving shank that allows the simultaneous pumping of grout during driving. The grout flows from the concrete pump into the grout reservoir and shank and then down the interior of the pile. The grout fills the interior of the pile and travels out the grout ports in the conical grouting shoe and alongside the DIP. The grout is pumped to maintain a grout return while creating the grout/soil interface to provide efficient skin friction along the friction DIP.
3) The pile is driven and grout is pumped continuously until the Plug & Drive socket end is nearly at the working grade. The driving resistance (time required to drive each meter increment) is observed during driving.
4) A second DIP section is then lifted into place so that the tapered or spigot end of the second DIP section is inserted into the socket end of the existing pile.
5) The driving / grouting process is repeated.
6) This process continues until the pile extends to a sufficient design depth in the competent bearing layer (bond zone) to develop the required frictional capacity through grout-to-ground bonding or encounters an end-bearing layer.
7) In the event that tension resistance is also required, a high-strength center bar is inserted into the wet grout to engage the frictional capacity and provide high tension resistance.
Installation Equipment
One attractive feature of the Ductile Iron Pile system is that it uses conventional earthwork equipment for installation including a single medium-duty excavator, hydraulic hammer and grout pump. The amount of specialized equipment and tooling is limited to the drive tools.
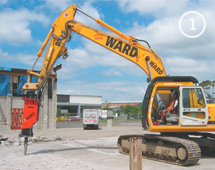
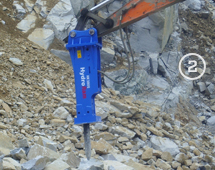
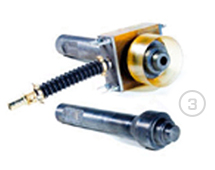
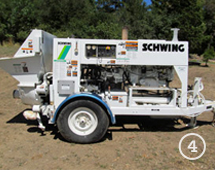
1) Base Excavator Machines
Base crawler excavators used for Ductile Iron Piles are typically in the 18 to 30 ton service or operating weight range. Alternatively, vertical-mast equipment with a hydraulic hammer may also be used for installations. The two primary factors for base excavator selection are the need to a) have sufficient height of the hammer to reach on top of the pile for driving and b) supply the required hydraulic power to the hammer. Therefore, compatibility of the base excavator with the hydraulic hammer is extremely important to both equipment performance and pile installation.
2) Hydraulic Hammer
The hydraulic hammer is a critical part of the Ductile Iron Pile installation process. Selection of the hammer is equally as critical to ensure 1) adequate hammer energy to drive the piles to obtain proper “set” conditions and 2) avoid overstressing and damaging the pile during driving. Factors that should be considered when selecting an appropriate hammer for DIP installation include:
- Pile diameter (98 mm, 118 mm or 170 mm)
- Grout cap diameter (if applicable) – (150 mm to 370 mm)
- Pile length
- Soil conditions (loose, dense, debris fill, etc)
- Pile design capacity
- Pile type:
- Friction
- End-bearing with “set” criteria
- End-bearing on refusal
It is important that the hammer flow requirements are properly matched with the base excavator for adequate functionality. In addition, connection of the hammer to the excavator will depend on the specifics of each piece of equipment. Specialty adaptors may be required to make the proper hammer-excavator connection and need to be investigated by the installer. Many installers elect to use side-mount hammer brackets to reduce the amount of overhead clearance needed for the system installation which also reduces the excavator size requirements.
3) Drive Shanks
Specialty drive shanks are required for installation of the Ductile Iron Piles. A solid (dry) drive shank is used for non-grouted pile installations and a grouting (wet) shank along with a grout box is used for exterior grouted pile installations. It is recommended that the wet shank primarily be used for exterior grouted pile installations and not for repeated end-bearing situations to avoid tooling damage. This damage potentially is largely because the combination of the high energy imparted during the driving process combined with the heating of the tooling that can occur without the presence of grout to act as a coolant during installation.
4) Grout Pump
A grout pump is required for installation of exterior grouted Ductile Iron Piles also for filling of the interior of the pile following installation of Non-Grouted piles. A colloidal pump is typically used for mixing neat cement (cement and water) for filling the interior of piles. A piston-driven, swing-tube concrete/grout pump is recommended for pumping sand-cement grout during the installation of Grouted DIPs. Although screw pumps can deliver high rates of delivery, they are not suitable for ductile iron pile installations because of the limited discharge pressure generated.
Like hammer selection, it is important that the grout pump be selected so that it is large enough to provide sufficient pumping pressures to introduce the grout at depth in the pile, but is not too large that it causes blockages in the line or over-pressurizes the system. Manufacturer recommendations indicate a maximum pumping pressure up to 1,000 psi (70 bars) and with a flow rate of 12 cfm (20 m3/h). The pump stroke size is also critical to avoid plugging. Pump strokes of ¼- to ½-cubic foot per stroke are well-suited for DIP installation.
During grouted DIP installation, the grout pump lines are connected to the grout box attached to the grouting (wet) shank in the hammer. Since the connection to the wet shank is a 2 inch (50 mm) connection, hose reducers are often required from the 4 inch (100 mm) or 6 inch (150 mm) line extending from the pump.
Quality Control
Results-driven Excellence
Despite the ease of installation of the Ductile Iron Piles, successful performance of the system relies closely on the level of quality control and testing undertaken during installation. The quality control / quality assurance activities consist mostly of monitoring items such as penetration depth, penetration rate, set criteria, grout pump strokes and termination depths. Full-scale load testing to verify capacity is also an important quality control aspect for the system.
Driving and Driving Rates
Quality control during DIP installation is largely focused on monitoring pile penetration and penetration rates during driving. Each section of Ductile Iron Pile is factory-marked in one meter increments to assist with monitoring the length of time required to drive 1 meter of pile into the ground. The rates of penetration are used as indicators of geotechnical resistance and pile capacity. For piles developing capacity in friction, the drive rates provide confirmation that the pile is penetrating into the competent bonding strata. For piles developing the capacity in end-bearing, the drive rates are measured (seconds/inch) to verify the adequate “set” criteria is achieved. Drive rates are monitored for both End-Bearing piles and also Friction Piles.
The figure below shows an illustration of driving rates with depth that is obtained for a pile.
The rate of penetration for Friction Ductile Iron Piles is used real-time during pile installation to determine the depth at which the bond layer (competent layer in which the bond zone is developed) is encountered. This is based on noting a marked increase in the driving resistance that is consistent with the anticipated depth of the bond layer. The pile is then driven a specified depth into the better layer based on the design requirements.
Depth of Termination
For End-Bearing Piles, the depth of termination is determined based on either refusal on a hard layer (rock) where further penetration or advancement of the pile is not feasible. Alternatively, piles may be terminated when a “set” criteria is met. The “set” criteria is defined as a limited amount of deflection observed while driving the pile for a particular time limit. Decades of installation and verification testing indicate that a “set” criteria of 1 inch or less of penetration in 50 seconds or longer is adequate to achieve the design geotechnical capacity for most design cases. Project-specific variations to set criteria are often made and established based on site-specific load testing.
Friction Ductile Iron Piles are not designed to be installed to a refusal layer or a specific “set” criteria. Instead, the grouted elements are designed to advance a particular depth into a competent strata to develop sufficient bonding length to generate the required design capacity through friction. Early refusal or “set” of a friction pile may still be acceptable for a compression pile depend on the design requirements.
Load Testing
Load testing is an important tool for verifying capacity of both End-Bearing and Friction piles. Load testing for end-bearing applications is performed in general accordance with ASTM D-1143-07 for static load testing of pile foundations (see load test picture). Alternatively, load testing for Friction piles may be performed in either compression in general accordance with ASTM D-1143-07 or in tension in general accordance with ASTM D-3689-07 to evaluate axial tensile load testing of piles (see load test picture). Tension testing is often an acceptable means to test the bond zone resistance for either tension or compression loads. It is often a preferred method for testing because it eliminates the need for numerous high capacity tension reaction anchors for a compression load test frame.
Ductile Iron Piles are typically load tested to 200% of the design load depending on project requirements. Local building codes establish the testing requirements and should be followed. The specific increments for loading often range from 10% to 25% of the design load depending on the standard with durations at each load ranging from 4 minutes to 60 minutes. A creep load is typically applied at 200% of the design load and maintained for a minimum of one hour and until the deflection is less than 0.01 inch/hour or 4 hour passes.
The results of the load tests are used to verify the design capacity of the Ductile Iron Pile. Many options for load test interpretation are used in the pile industry including the Davisson Offset, Brinch-Hansen Method and the Butler-Hoy Criteria. Determination of the acceptance requirements need to rely on the project performance specifications or local code interpretation.
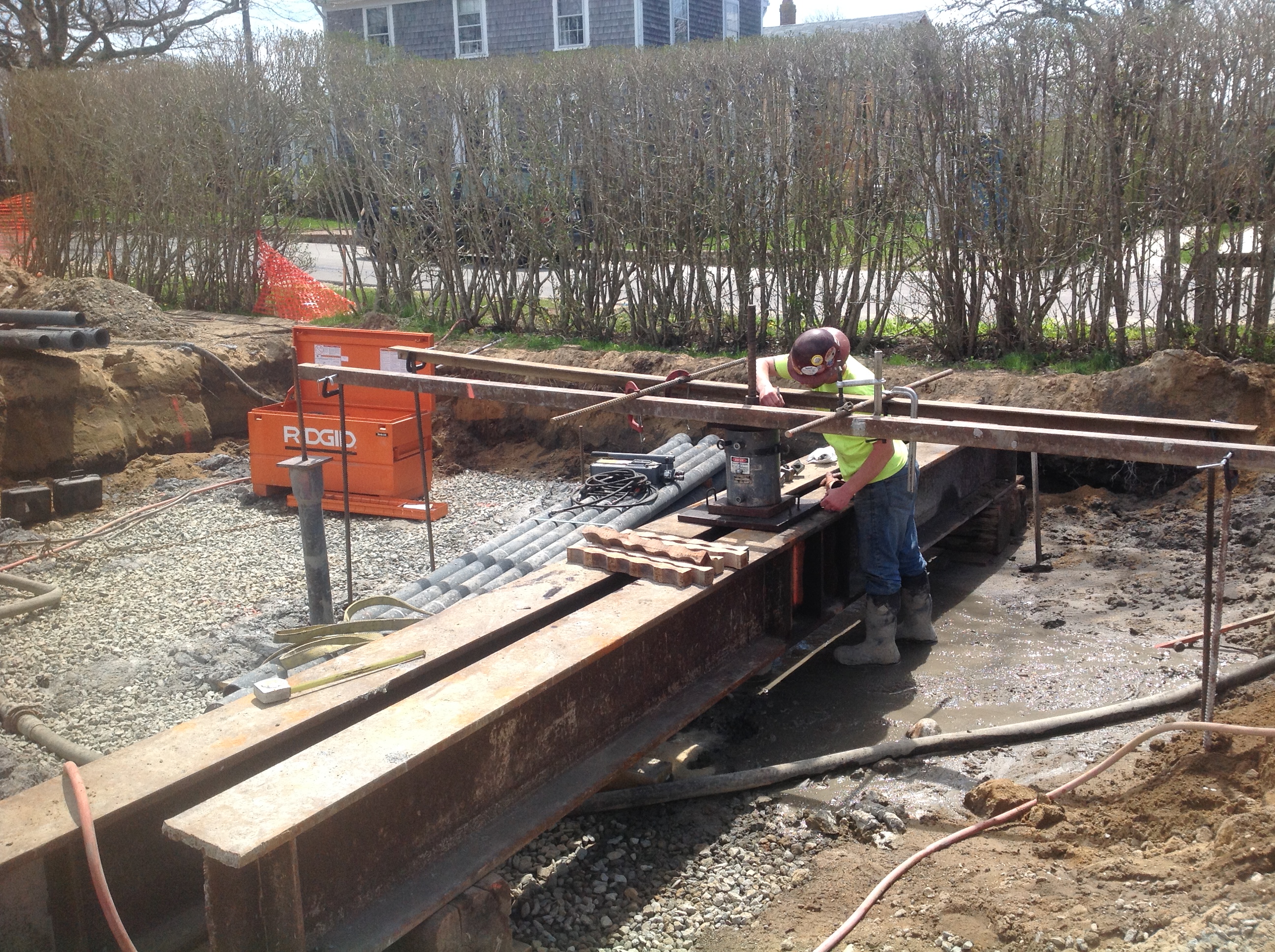
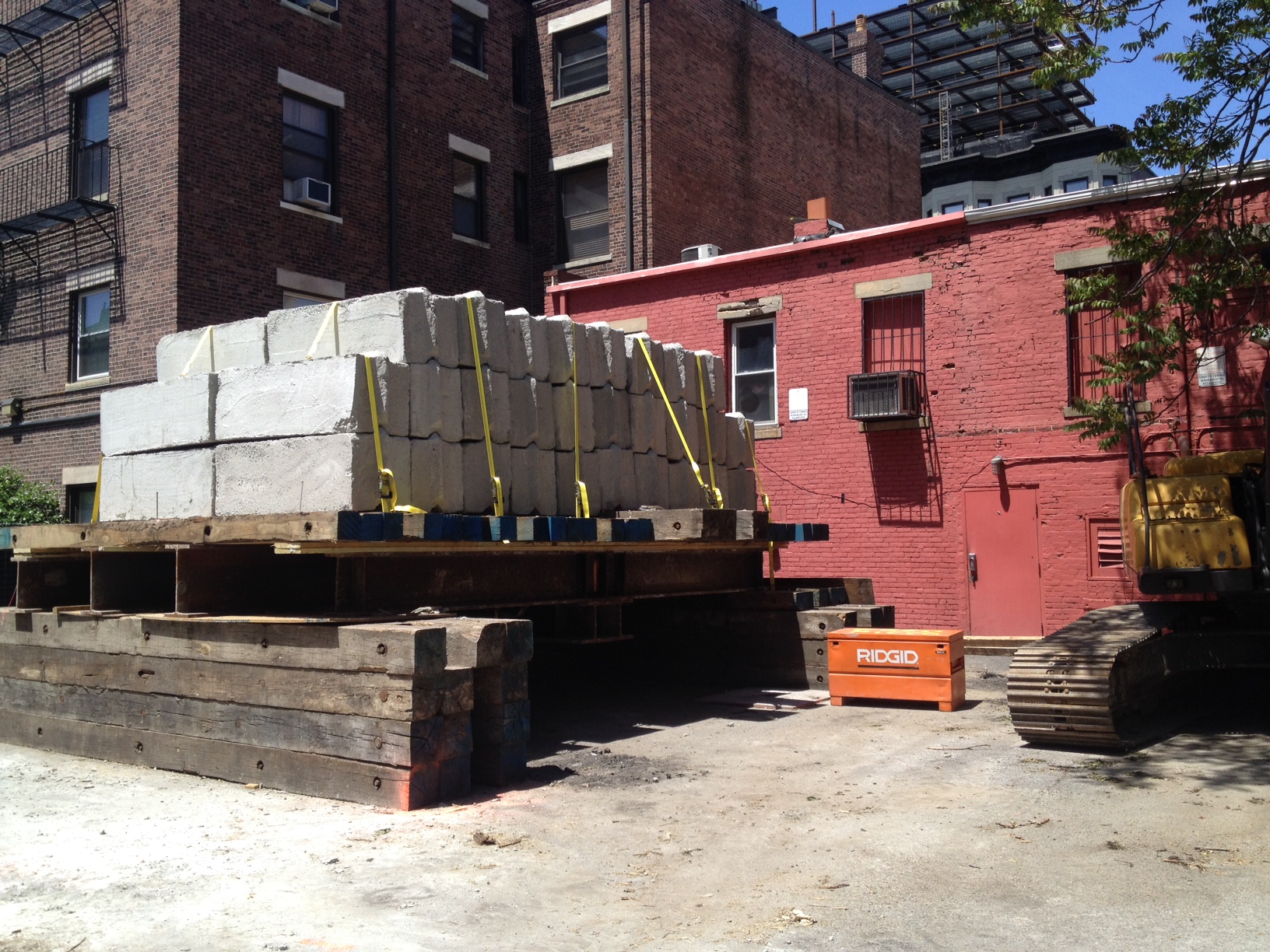
Grout Testing
Grout testing is often performed to verify that the grout strength reaches the minimum design requirement. For neat cement grout, often used to fill the interior of non-grouted piles, grout cubes are made during the grouting operation. For sand-cement grout used during the installation of grouted piles, it is recommended to use 4” x 8” concrete cylinders as the most representative test to evaluate the strength of the mix.