Ductile Iron Pile Products
Ductile Iron Piles (DIPs) are a simple, fast and highly effective modular, low-vibration driven pile system comprised of high-strength ductile cast iron. Pile sections are connected by a proprietary Plug & Drive joint system, eliminating the need for field welding and splicing while providing a high degree of stiffness and full moment capacity. With the use of an excavator fitted with a hydraulic hammer, piles are installed in quick succession leading to fast and easy installation.
Ductile Iron Piles are manufactured by Tiroler Rohre, GmbH of Austria from ductile cast iron, which provides high-impact resistance to the low amplitude, high frequency installation energy. The material also exhibits high ultimate strength, elastic limit and ductility as well as superior corrosion resistance when compared with traditional steel piles.
Ductile Iron Piles are well-suited for supporting loads in a variety of problematic soil conditions including both cohesive and non-cohesive soils and can also resist compression and tension loads.
VIEW THE DUCTILE IRON PILE BROCHURE
Piles & Accessories
End-bearing & Friction Piles
Ductile Iron Piles have been manufactured by Tiroler Rohre GmbH (TRM) in Austria for over 35 years. Each modular pile section features a Plug & Drive connection consisting of a tapered socket with an internal shoulder for full engagement at one end and a tapered spigot at the other end. This allows the individual pile sections to be connected together to form a pile shaft of virtually any length without the use of special tools. The connection is formed by elastic deformation of the ductile iron and by cold welding of the friction surfaces. This joint exhibits high-compressive strength and superior resistance to bending, such that the rotational stiffness of the joint is greater than the main pile shaft. This connection method eliminates the need for threads, couplers, pins and keys and field welding/splicing on the job site.
Ductile Iron Pile installation methods consist of either dry (no exterior grout) or wet (continuous grouting operation during installation) installations. Additionally, both options can develop load-carrying capacity in either friction in competent soils, end-bearing on very hard ground/rock or a combination of both. The specific pile materials and accessories depend on the type of installation and mechanism for load resistance. Both methods utilize a unique combination of installation speed and high capacity that results in a highly cost-effective deep foundation system.
End-Bearing Piles
Ductile Iron Piles installed for end-bearing are driven through compressible and unsuitable soils to transfer their load to a hard stratum below. They derive most of their load-carrying capacity thru resistance along the portion of the shaft in competent soil and at the toe of the pile. End-bearing piles may be installed using a dry installation method without continuous grouting during installation (as pictured) or as the wet installation method with oversized pile shoes and continuous pumping of exterior grout.
Friction Piles
Ductile Iron Piles installed as friction piles penetrate poor soil conditions and develop the majority of the load-carrying capacity in frictional resistance along the perimeter of the pile shaft in the competent strata. While some friction piles use a dry installation method (without continuous grouting) and develop strength through the interface between the soil and the roughened exterior of the ductile iron pile shaft, the majority of friction piles utilize oversized conical drive shoes and exterior grout to encapsulate the pile during driving for very effective grout to ground bonding. The oversized cap results in significant expansion (and densification) of the competent soil while the grout-to-ground bonding provides a highly efficient mechanism for load transfer.
Ductile Iron Piles Material Specifications
Ductile Iron piles are typically manufactured in standard (usable) lengths of 5 meters (16.4 feet). Overall pile lengths including the bell (socket) are slightly longer and range from 16.9 ft (5.15 meters) to 17.2 ft (5.25 meters). Piles are available in multiple diameters and wall thicknesses to suit project needs. Details of the dimensional characteristics are provided below:

All Ductile Iron Piles are manufactured in 5 m (16.4 ft) lengths.
Product Accessories
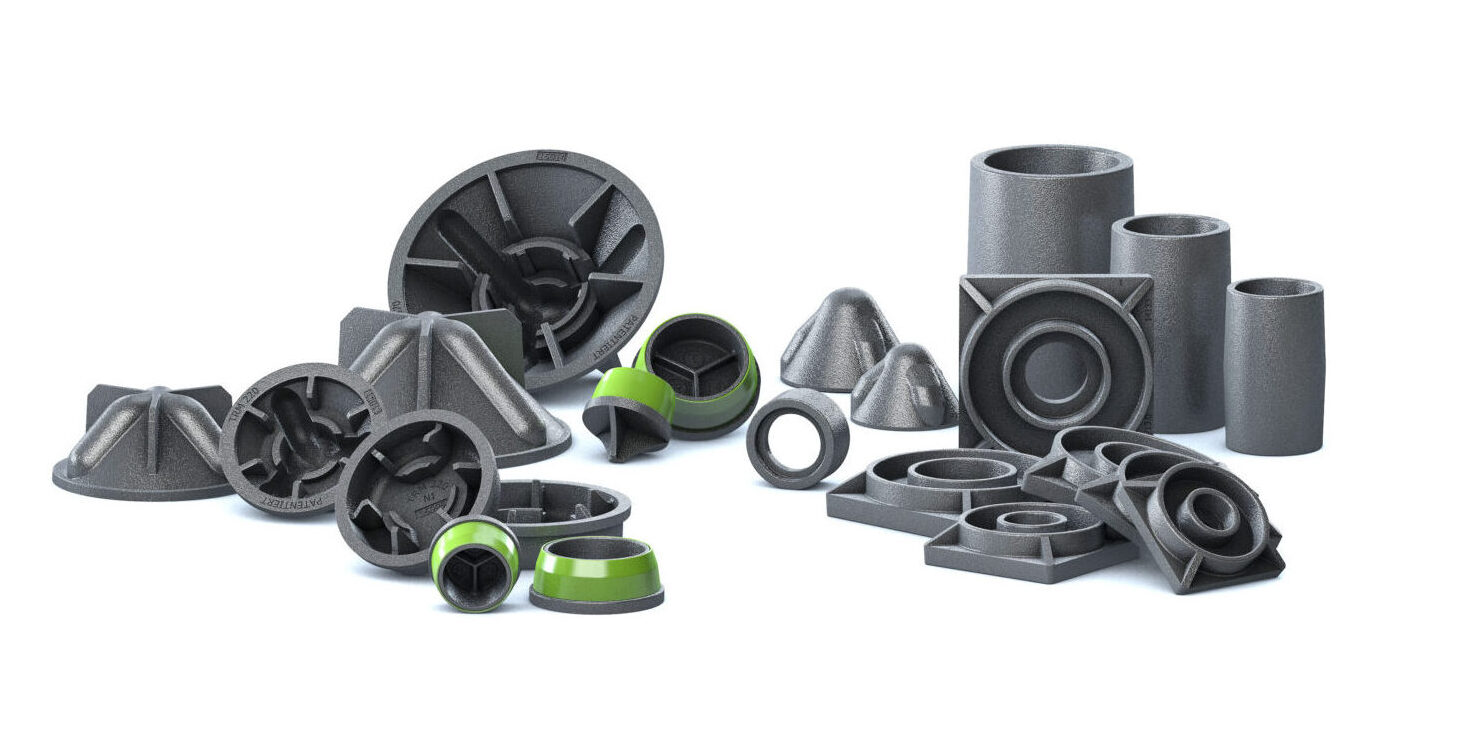
The same pile sections are used for both end-bearing and friction applications. However, the various accessories are specific to the type of application and method for loading resistance:
Flat End Drive Shoe
Standard drive shoes for piles installed using the dry installation method.
Rock Point
Alternative drive shoes for dry installation methods, typically for end-bearing (non-friction) piles, used when driving through harder material such as partially weathered rock or glacial till.
Heavy-Duty (HD) Flat Drive Shoe
Heavy-duty (HD) flat drive shoes for dry piles are used when driving through hard conditions such debris fill, partially-weathered rock or glacial till for greater durability during driving. HD caps are also used in very soft soils to reduce the potential for dislodging of the drive shoe during driving.
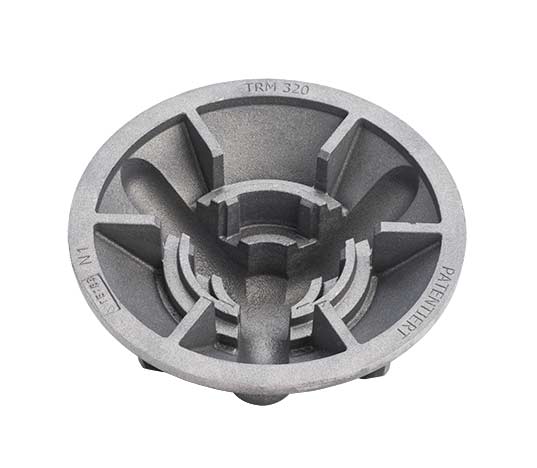
Conical Grout Shoe
Conical grout shoes are used for installation of exterior grouted (wet installation) piles. Grout shoes have a larger diameter than the pile, creating an annulus around the pile which enables the placement of fine-aggregate concrete (grout) to encapsulate the full length of the pile shaft. Grout shoe diameters range from 150 mm (5.9 in) to 370 mm (14.6 in). Appropriate shoe sizes depends on the pile size, soil conditions, hammer size and desired design capacity.

Coupler
A coupler is used to connect two partial pile sections in place of the standard spigot and socket connection. Couplers are most often used when piles are driven in low headroom environments where pile sections must be cut for overhead access. Couplers are not required for standard applications with full-length pile sections utilizing the Plug and Drive connections.
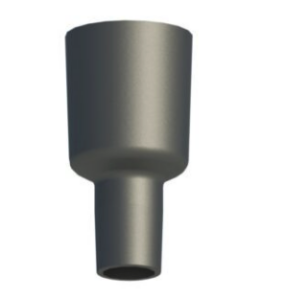
Converter
A Converter is used to switch from a Series 118 pile to a larger Series 170 pile. The Plug and Drive converter is installed into the bell of a Series 118 pile and a new Series 170 pile is then inserted and driven. The converter is often used for situations where a larger pile size is required at shallow depths to resist lateral loads, but the axial capacity does not require the larger pile for the full length.

Drive Shanks and Grout Box
A drive shank is a specialized attachment that facilitates the driving of the piles using conventional hydraulic percussion (breaker) hammers. Drive shanks are specially fabricated and hardened to withstand the high driving stresses during installation. Drive shanks are available as 1) solid or dry shanks for installation of dry piles (ungrouted during driving) and 2) wet or grouting shanks to facilitate grout injection into the pile interior during installation of grouted piles. The grout box is designed to surround the wet shank and provide a grout reservoir during grouted pile installation. A wet shank and grout box are used in concert.