Packaged Solutions – Ductile Iron Piles Combined with Ground Improvement
If you’re like us, you’ve been amazed to see how quickly the construction industry has embraced ground improvement technologies for supporting structures over the past 20 years. It seems like there are now as many different ground improvement installation methods as there are geotechnical specialty contractors to install them! One thing is clear, ground improvement systems are proven to provide a low-cost and effective method for foundation support and are here to stay.
While many projects benefit from ground improvement, there are times when certain features of new construction require taking the next step to deep foundations. DuroTerra has worked with many geotechnical specialty contractors to provide Ductile Iron Piles (DIPs) at select foundation locations on ground improvement projects. Some examples are as follows:
- Most commonly, low-vibration DIPs are used for new foundation support near existing structures that can’t tolerate the higher-vibrations associated with some ground improvement techniques.
- Perimeter wall foundations that abut existing structures, requiring deep foundations to transfer building loads below the zone of influence of older foundations.
- Structures that have specific features like large mats, equipment pits, interior tanks, or other building components that are too heavy to be supported on ground-improvement.
- Unexpected subsurface conditions, like urban or debris fill, that can’t be penetrated with ground improvement techniques.
- Subsurface conditions where unsuitable soils extend to depths beyond the treatment depth for ground improvement systems.
- Logistical constraints on a jobsite that won’t allow larger ground improvement equipment to access certain parts of the required work area.
- Interior scopes of work where overhead restrictions limit the access of ground improvement equipment.
Many ground improvement contractors have the experience and equipment to install Ductile Iron Piles, making the addition of DIPs to their ground improvement projects a simple task. Requiring only a medium-sized excavator and a percussion hammer, some of the largest ground improvement contractors in the US are quick to implement this FAST. SIMPLE. SAFE.™ solution to provide comprehensive geotechnical solutions to their customers. Below are a few examples of projects that combined ground improvement with Ductile Iron Piles. If you have additional questions or would like to evaluate feasibility for your project – contact us here.
PROJECT EXPERIENCE – BOLLES SCHOOL
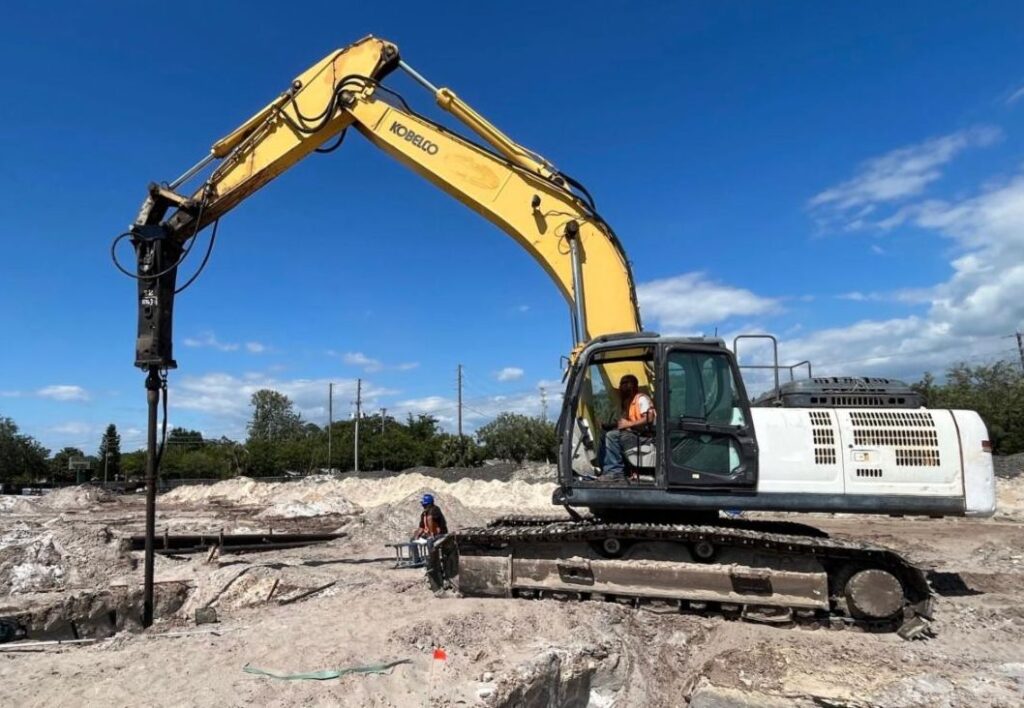
EarthTech installing Ductile Iron Piles
The Bolles School campus features a synergy of foundation solutions that were recently installed to support construction of the new Center for Innovation Building, located along the St. Johns River in Jacksonville, Florida. The soils at the site were reported to consist of loose to very loose sands extending to depths of approximately 65 feet below grade followed by Florida limestone. These soils would be subjected to excessive settlements if supported on conventional shallow foundations. To limit settlements to allowable tolerances, Menard USA was hired by Stellar, the project general contractor to provide Controlled Modulus Columns (CMC®) rigid inclusions at the site. CMCs, specially designed cementitious lean mix elements installed using a displacement auger, were extended from the bottom of the foundations to the competent limestone layer.
A significant challenge to construction was the steep slope along the western portion of the site. The rig that was being used to install the CMCs was not able to safely access the locations adjacent to the slope. Future site development plans included the construction of a retaining wall to support the construction of building foundations along the slope. However, the wall construction was to follow the installation of the CMCs. Due to construction schedule constraints, Earth Tech, a Menard Company acquired in April 2022, was brought on board to install Driven Ductile Iron Pile (DIP) elements adjacent to the steep slope.
The Series 118/7.5 DIPs used for this project are most commonly used as a deep foundation element. In this case the DIPs were specifically designed to serve as a type of rigid inclusion. Installed using a medium-sized excavator, this provided great flexibility with installations and allowed for safe access along the slope prior to the installations of the retaining wall. Similar to CMCs, they also produce limited spoils and vibrations during installations. By creatively incorporating DIP elements into the rigid inclusion deign, the Menard/Earth Tech team was able to complete the ground improvement construction by minimizing impact to regular school operations and minimizing significant delays and modifications to the construction schedule. This project is a great example of good team effort by all parties to successfully complete the job. (Thanks to Venkata Muppana, P.E., of Menard USA for contributions to this story)
PROJECT EXPERIENCE – ENTERGY SUBSTATION UPGRADES
Upgrades to the existing Entergy Services 115kV Substation included foundations for new transformers, transmission line towers and other supporting structures. Many foundations were isolated, lightly-loaded foundations, while others included larger mat foundations. Subsurface conditions encountered at the site consisted of soft to medium stiff silty clay and loose silt extending up to 11 feet below grade followed by very soft highly-plastic clay extending up to 46 feet below grade. The clay was underlain by medium dense sand to the maximum explored depth of 50 feet. Groundwater was about 10 feet below grade.
Loading demands on many of the foundations required compression, tension and lateral resistance. The project was originally specified for pile caps supported by helical piles. Inadequate field performance during load testing combined with a high foundation cost steered the design team toward alternative options.
Representatives of Peterson Contractors, Inc. and Geopier Foundations worked with the project team to develop an approach featuring Geopier® ground improvement combined with Ductile Iron Piles. The Geopier Impact™ system was planned for support of isolated, lightly-loaded shallow foundations to provide settlement control and improved bearing support, while Ductile Iron Piles were designed to support the more heavily-loaded mat foundations by providing compression, tension and lateral load resistance.
The Ductile Iron Pile design featured Series 118/7.5 piles (118 mm diameter with wall thicknesses of 7.5 mm) with an oversized 220 mm conical grout shoe. The oversized grout shoe creates an annular space during driving of the pile. Sand cement grout is continuously pumped through the wet drive shank, down through the pile and out through grout ports in the drive shoe to completely encapsulate the pile with grout during driving. The end result is a fully-grouted pile that develops substantial grout-to-ground bonding for friction capacity. Piles were driven to completely penetrate the very soft clay and extend into the medium dense sand a minimum of 15 feet to develop sufficient frictional capacity in the sand layer. Following installation, a high strength 1” Grade 150 ksi threadbar was inserted into the full length of pile to resist tension loads. The Ductile Iron Piles were designed for working loads of 66 kips (compression), 37 kips (tension) and 5 kips (lateral). Peterson Contractors, Inc. performed load testing at the site to confirm the design performance of the friction Ductile Iron Pile solution. Following successful load testing, a total of 94 production piles were installed with lengths on the order of 65 feet in less than 2 weeks on the site.
The use of the DIPs provided an economical approach to supporting the large substation foundations with compression, tension and lateral demands. Combined with the Geopier ground improvement for the lighter foundations, the design build solution resulted in substantial value to the project. Read more.