Ductile Iron Pile – Common Myths
Myth #1
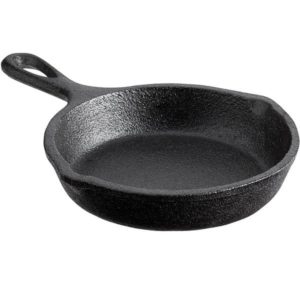
When many people think of “cast iron”, besides thinking of their trusty frying pan, images of old water or sewer pipe might also come to mind…Thoughts of cast iron products that have been in construction since the 1800s, and are most commonly linked with the horizontal transmission of water and waste. These early materials were often brittle and could not resist impact without damage. How on earth could these materials be used as pipe sections driven vertically into the ground for structural foundation support?
The reality is that the science behind cast iron materials have come a long way since the early days of cast iron. Production of the original cast iron or gray cast iron generated inclusions of graphite in a lamellar form – meaning the graphite material was oriented in flat plate- or flake-like structure. The lamellar form of graphite flakes often led to stress concentrations and cracking – resulting in the brittleness and low strength often attributed to cast iron.
Over the last half a century, metallurgists discovered that the addition of magnesium to the molten cast iron immediately prior to pouring into the molds would produce crystallization of graphite in spheroidal or nodular form rather than the weak graphite flakes. These spheroidal graphite inclusions reduce the potential for stress concentration created by the graphite flakes to dramatically improve many of the properties of the traditional cast iron – and ductile cast iron is created. The improvements include increases in the material strengths including ultimate and yield strength, tensile strength and flexural strength. The creation of the spheroidal graphite form of iron or ductile cast iron also enhances the impact resistance for drivability and toughness while still maintaining the cast iron qualities for castability.
Our manufacturer partner, Tiroler Rohre GmbH (TRM) of Austria has been using these advancements in ductile cast iron properties and castability to produce the highest quality of ductile iron in pile form for over 40 years. Additionally, TRM’s Ductile Iron Piles have a uniquely engineered bell & spigot shape to provide a Plug and Drive connection that forms a moment-resisting connection during driving. The piles are cast with an enlarged “bell” that handles the high impact driving energy with significant resistance to breakage. The unique Plug and Drive connection has been used to construct piles on hundreds of projects across North America disproving the myth that Ductile Iron Piles are brittle and weak.
Was this worth the read? Please let us know – we want to hear your feedback (info@duroterra.com). Look for the March DuroTerra Dialogue, where we’ll dispel more myths about Ductile Iron Piles. Until then, we invite you to review some recent projects where our installation partners used DIPs to construct FAST, SIMPLE, and SAFE foundation systems for their customers.
Relevant projects
A new tower bed addition at the existing hospital complex required the construction of a pedestrian bridge to connect the two buildings. The bridge, spanning a wide arterial street, required 13 new foundations with loads up to 1,100 kips (compression), 150 kips (tension) and 150 kips (lateral). Geotechnical conditions consisted of up to 15 feet of sand underlain by as much as 30 feet of soft to stiff clay underlain by limestone bedrock at variable depths. Earth Tech Geotechnical Construction worked with the project team to consider various foundation options and ultimately landed on Ductile Iron Piles as the best combination of performance, ease of construction, and low cost. Exterior grouted Series 118/7.5 Ductile Iron Piles installed with a 220 mm grout shoe and a high strength center bar were designed for allowable loads of 75 kips (compression), 30 kips (tension) and up to 7.7 kips (lateral). Earth Tech installed 183 piles for the project close to both existing buildings and the busy street that separated the buildings. Due to the highly variable bedrock conditions, piles varied from 34 to 107 feet in length – making the modular Ductile Iron Pile system ideally suited to handle the highly variable rock.
Construction of the Hood Park redevelopment effort included a new storage pavilion and elevated green space / pedestrian bridge. With 18 feet of urban fill and 4 feet of peat and organics, geotechnical engineers at Haley & Aldrich, Inc. knew that shallow foundations would not be feasible and explored deep foundation options for foundation support. In addition to structure support, the deep foundation system needed to be designed to resist the potential for loss of confinement in the upper portion of the pile due to an adjacent future excavation. The project team selected exterior grouted Ductile Iron Piles to support the structure and transfer building loads to the underlying glaciomarine sand and clay and glacial till. The exterior grouted Series 118/9.0 piles were designed for an allowable capacity of 40 tons. Full-scale load testing performed to 90 tons (225% design load) showed only 0.33 inches of deflection at the maximum test load and strain gauges verified the transfer of load to the bond zone below the fill and organics. Phoenix Foundation Company, Inc. installed the 128 production piles in only 9 working days to cut the project schedule in half.