FAST. SIMPLE. SAFE.®
You might have seen our tag line in our advertisements or read last month’s Dialogue where we introduced the following three terms that so accurately describe TRM’s Ductile Iron Piles:
- FAST – the low vibration, driven system is installed much faster than micropiles and other deep foundation systems.
- SIMPLE – the versatile system can be installed using a dry or wet (grouted) method, yet either is much less complicated to install than other deep foundation techniques (which also contributes to being FAST!)
- SAFE – without rotating drill tools or torque motors or large vertical mast rigs or crane-mounted leads with suspended and often lengthy pile sections, the system is extremely safe to install.
This month we draw attention to the SIMPLE nature of the Ductile Iron Pile system. And in this industry, simple is a very good thing. The simplicity comes in a few different forms. Ductile Iron Piles are simple to design. Engineering design approaches rely heavily on industry experience and methods with similar systems like traditional drilled micropiles and driven piles to estimate both structural and geotechnical capacities. Then there’s the simple nature of the installation, which is what most of our installers think of. Many piling systems like micropiles require complicated, purpose-built drill equipment and highly-experienced operators to successfully perform installations. In contrast, the Ductile Iron Pile system uses common earthwork equipment consisting of medium-sized (20 to 30 ton) excavators and percussion demolition hammers to perform the installation. Operators new to installation of Ductile Iron Piles quickly and effectively learn the techniques for proper installation. Whether the system is installed using dry pile installation methods (certainly the easiest) or even a wet (exterior-grouted) installation method, Ductile Iron Pile construction is remarkably straightforward for both new and experienced crews.
Looking for examples? Check out the following project highlights that illustrate the simplicity of the installation. Want to benefit from the SIMPLE installation on your project, reach out to us today for a complementary feasibility assessment or to discuss equipment needed to get started.
PROJECT EXPERIENCE – DAL-TILE SILO FOUNDATION
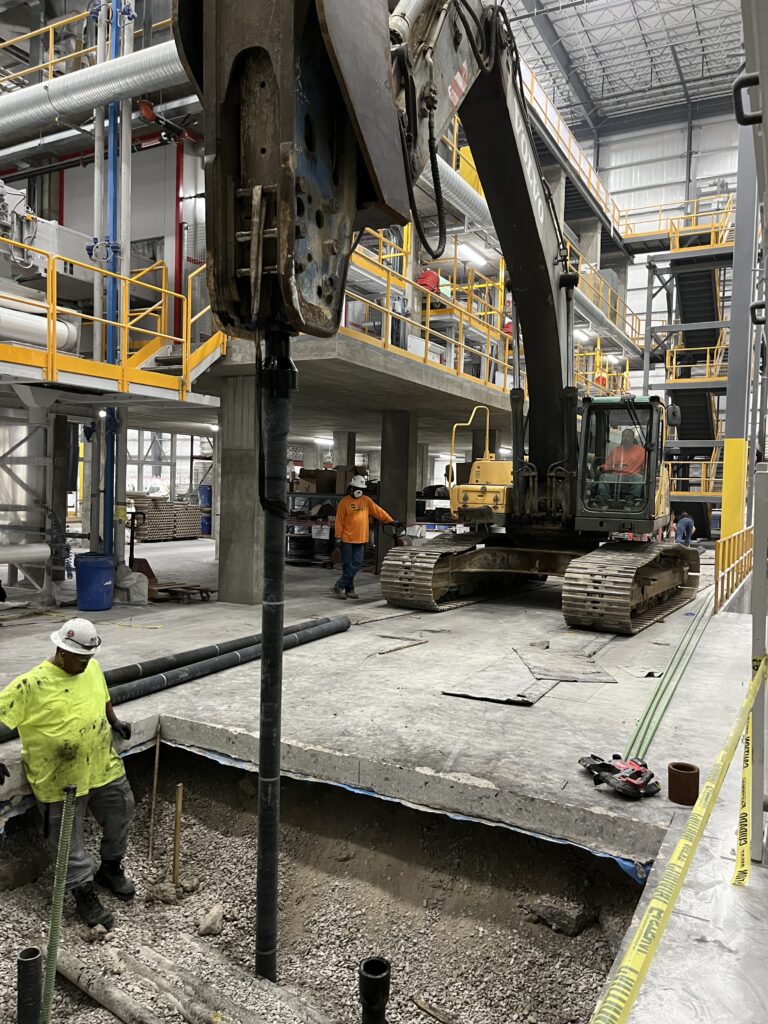
Installation of Ductile Iron Piles in a Tight Access Area
Additions to the Dal-Tile manufacturing facility included a new raw-product storage silo. The new silo was planned adjacent to existing silos inside the existing manufacturing plant. With loads of over 800 kips (compression) and 200 kips (uplift), silo support required a deep foundation system to transfer foundation loads through 60 feet of soft to very stiff clay to the underlying rock. Ductile Iron Piles were selected over micropiles due to the simple installation process including both the clean, dry installation method as well as the elimination of drill spoils management. The Ductile Iron Piles were installed within limited overhead clearance and limited access (narrow aisle widths of 12 ft) by a crew with limited experience with the system. Series 118/9.0 piles were installed to terminate on rock to develop 40 tons of capacity in compression and up to 14 tons in tension. Despite being their first project with the system, the simple construction process enabled Chris-Hill Construction to install close to 1,000 LF of piles in only two days.
PROJECT EXPERIENCE – THE ADELE

Ductile Iron Pile installations at The Adele in Washington, D.C.
The Adele redevelopment project involved the construction of a new 8-story residential building three blocks north of the White House. The original structure was razed except for the exterior façade of the lowest two floors. There was nothing simple about coordinating the construction on the 5,025 sq ft footprint site that was bordered by buildings on both sides at the property line, the historic façade at the front and a nearby building to the back. The project team required a low vibration foundation support that could work within the very constrained site.
Soil conditions consisted of up to 8.5 feet of mixed urban fill underlain by terrace deposits consisting of loose to medium dense sand and firm to stiff clay to depths up to 35 feet. Loose to very dense residual silty sand and silt were then encountered to depths of 35 to 40 feet followed by weathered rock.
The GeoStructures design-build team worked closely with the project team to develop a simple solution consisting of grade beams and pile caps supported by Ductile Iron Piles. Materials for the modular DIP system were easily transported to the site and stacked to limit laydown requirements. Series 118/7.5 (118 mm OD with 7.5 mm wall thickness) piles were installed through the fill, terrace and residual deposits to terminate on weathered rock to generate a 40 ton (compression) capacity. In locations where tension resistance was needed, the wet installation method was used with a 220 mm grouting shoe and the Series 118/7.5 pile along with a center bar to construct an 8.5-inch diameter grouted displacement pile. Load testing showed less than ¼-inch of deflection at the design load. A total of 145 piles were installed to support the new structure. While working on constrained sites is never simple, the Ductile Iron Piles certainly did its part to limit the complexity of the foundation construction.